Oct 20 2017
Case Study: Flexi-Coil® Wax Removal in West Africa
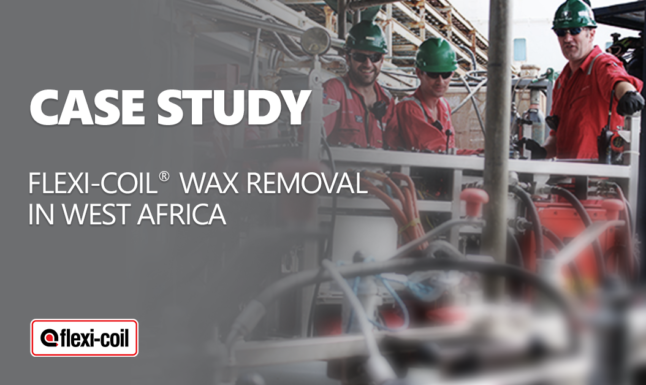
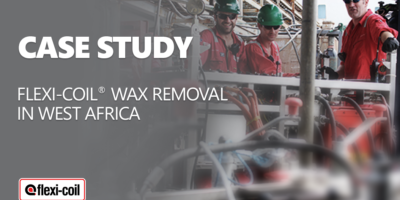
Flexi-Coil® succesfully removes wax in West Africa subsea riser & flowline
100% Oil production uplift
Overview
An O&G operator in West Africa had a severely reduced flow path from a subsea well tieback due to heavy internal wax deposition in the pipeline and riser. The reduced flow path and high differential pressure resulted in shutting in the well and stopping production in order to attempt a remediation solution. Conventional methods were considered but deemed ineffective.
Challenge
The riser and flowline were narrow bore at 4” OD and close to being completely blocked. The heavily restricted flow path would make it difficult to displace the wax deposit over 200m vertical displacement and 550m step out distance. The receiving platform had limited availability of facilities and small area of deck space to rig up the Flexi-Coil® unit and support equipment. Conventional cleaning using pigging technology and chemical soaking was either not possible, too costly or ineffective. The narrow bore and limited working space made intervention using conventional coil tubing impractical.
Solution
The compact footprint, ability to traverse multiple tights bends and powerful cleaning tools made Flexi-Coil® an ideal fit. Flexi-Coil® has integral dynamic pressure and isolation, which ensures control of the coil and annular flow of fluids to and from the surface package. Brine was used to assist displacement of wax solids back to surface. A filtration package separated the wax particles and recirculated the fluid ensuring containment and zero spills. Wiper trips were made to minimize build-up of wax behind the coil and maintain clear flow.
Result
- Over 45bbls of wax deposits successfully cleaned and returned to surface.
- Production Flow tests performed immediately post clean showed steady state 100% production improvement.
- Operation completed safely without LTI within 10 days of arrival on platform including rig up/down.
- Back to parent metal deep clean of riser & pipeline bore
Value to client
- Immediate and sustainable production improvement.
- Rapid return on investment using new & innovative technology.